The world of plastic manufacturing is changing fast, thanks to more use of artificial intelligence (AI). The need for better precision, efficiency, and sustainability is pushing the industry forward. AI is key in making the next generation of THY Precision injection molding machine types better.
But have you thought about how this new technology is changing how we pick, set up, and use injection molding machines? Let’s dive into how AI is changing the future of making plastics.
Key Takeaways
- Discover how AI is transforming the injection molding industry and driving the development of next-generation machine types.
- Understand the common classifications of injection molding machines and the challenges in selecting the right equipment.
- Explore the integration of AI for enhanced machine selection, configuration, and optimization to boost efficiency and precision.
- Learn about the impact of Industry 4.0 and the Internet of Things (IoT) on the future of injection molding machine types.
- Gain insights from real-world case studies and success stories showcasing the power of AI in transforming plastic manufacturing.
Introduction to Injection Molding Machine Types
THY Precision is a top provider of industrial injection molding equipment. We know how crucial it is to pick the right machine for your needs. Injection molding makes a wide range of plastic products. The machine type you choose affects your process’s quality, efficiency, and cost.
At THY Precision, we have a wide range of injection molding machine types. These include all-electric, hybrid, and hydraulic models. Each is made for different needs in your injection molding business. Knowing the differences helps you pick the best for your process.
Common Classifications of Injection Molders
The main types of injection molding machines are:
- All-Electric Injection Molding Machines: These machines use electric motors for injection, clamping, and ejection. They offer precise control, save energy, and need less maintenance.
- Hybrid Injection Molding Machines: Hybrid machines mix electric and hydraulic tech. They give you the speed and precision of electric motors with the power of hydraulic systems.
- Hydraulic Injection Molding Machines: These machines use hydraulic power for injection, clamping, and ejection. They are strong and versatile for many applications.
Each injection molding machine type has its own benefits. They suit different production needs, part sizes, and materials. With THY Precision’s help, you can find the best injection molding machine types for your business. This ensures your plastic injection molding is efficient.
Injection Molding Machine Type | Key Features | Typical Applications |
---|---|---|
All-Electric | – Precise control and repeatability – Energy-efficient operation – Reduced maintenance | – Medical devices – Electronics – Precision components |
Hybrid | – Combines electric and hydraulic advantages – Faster cycle times – Versatile performance | – Automotive parts – Consumer goods – Household items |
Hydraulic | – Robust and powerful operation – Suitable for large parts – Versatile material compatibility | – Outdoor equipment – Industrial components – Large-scale packaging |
Knowing the features and capabilities of these injection molding machine types helps you make a smart choice. Contact THY Precision to learn about our injection molding machine types. We can help you improve your manufacturing process.
Challenges in Selecting the Right Injection Molding Machine Type
Choosing the right injection molding machine is tough. There are many types out there. You need to think about part complexity, how much you plan to make, what materials you use, and how efficient you want to be.
Finding the right balance is key. Complex parts need special features like closed-loop controls. You also want to make things efficiently and save money. This makes choosing a machine harder.
Manufacturers face these challenges to pick a machine that makes high-quality parts efficiently. It’s important to know about the latest in injection molding machines. This helps make a choice that benefits your business.
Key Considerations | Importance |
---|---|
Part Complexity | Determines the required machine features and capabilities |
Production Volume | Impacts the selection of machine size, output, and efficiency |
Material Requirements | Affects the choice of machine type, screw design, and temperature control |
Energy Efficiency | Plays a crucial role in reducing operating costs and environmental impact |
By looking at these factors, manufacturers can pick the best injection molding machine. This ensures they work well, make quality parts, and save money.
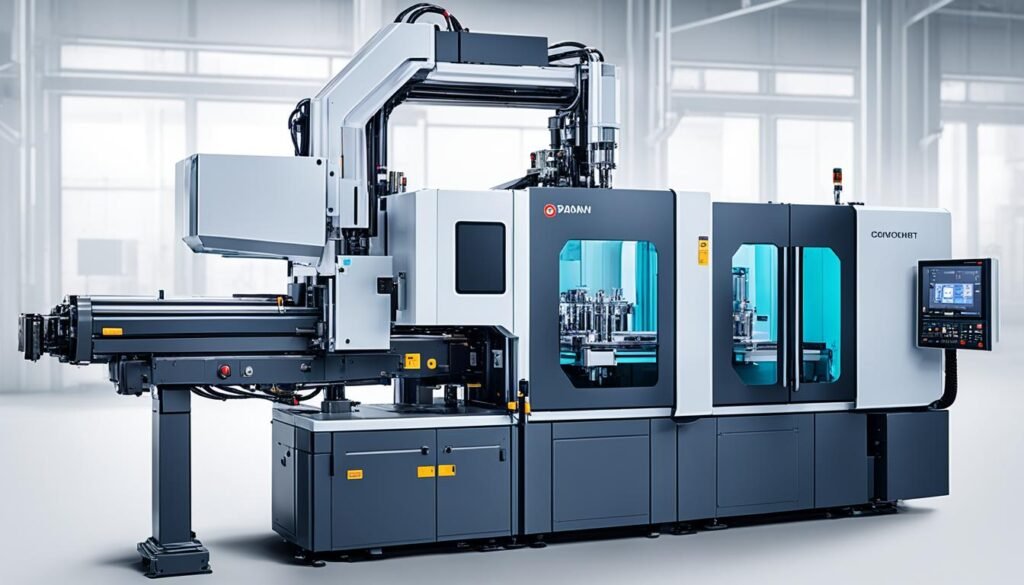
“Selecting the right injection molding machine type is crucial for the success of any manufacturing operation. It’s a complex decision that requires a deep understanding of the project’s requirements and the latest advancements in injection molding technology.”
The Role of Artificial Intelligence
The injection molding industry is changing fast, and artificial intelligence (AI) is key in picking and setting up injection molding machine types. AI systems are changing how manufacturers pick and improve their plastic injection molding machines. They help solve the problems that come up when making these big decisions.
AI-Powered Machine Selection and Configuration
AI is changing how manufacturers find the best injection molding machine types for their needs. It looks at lots of data like part design, material types, and what’s needed for production. Then, it gives advice on the best injection molding machine types for a job.
AI also helps set up the injection molding machine to make parts consistently and well. This smart way of making decisions helps avoid the mistakes of picking machines by hand. It makes things run smoother, faster, and better.
Key Benefits of AI-Powered Injection Molding Machine Selection and Configuration |
---|
|
Adding AI to pick and set up injection molding machine types is a big deal for the industry. It lets manufacturers make smart choices based on data. This brings new levels of efficiency and quality to their work.
“AI-driven solutions are transforming the way manufacturers approach the selection and optimization of their injection molding machines, helping them overcome the challenges that often arise in this critical decision-making process.”
Injection Molding Machine Types and AI Integration
The world of plastic injection molding is changing fast. Now, injection molding machine types are getting smarter with AI technology. This change is making production better, faster, and greener.
AI is making a big impact on plastic injection molding machines. It helps with real-time data, predictive analytics, and control. This means injection molding machine types work better, make fewer mistakes, and produce more.
THY Precision is a top name in injection molding machine types. They’ve added AI to their machines. These machines use smart algorithms to check and improve production, making things smoother.
Injection Molding Machine Type | AI Integration Benefits |
---|---|
All-Electric | Precise control, energy efficiency, reduced maintenance |
Hybrid | Improved cycle times, optimized energy consumption, enhanced precision |
Hydraulic | Increased flexibility, real-time process monitoring, predictive maintenance |
AI is changing the future of plastic production. Companies using AI in injection molding machine types will lead the way. They’ll meet market demands better.
“The integration of AI into our injection molding machine types has been a game-changer for our business. We’re now able to achieve unprecedented levels of efficiency, quality, and sustainability in our plastic production processes.”
– THY Precision, CEO
Industry 4.0 and the Future of Injection Molding
The injection molding industry is on the brink of a big change thanks to Industry 4.0. Now, injection molding machines are linking up with the Internet of Things (IoT). This is making production more efficient, improving quality, and helping with predictive maintenance.
At the core, machines are now connected to IoT networks. This lets companies use real-time data to make the manufacturing process better. They can keep an eye on machine performance and predict when they might need maintenance. This helps manufacturers improve continuously and stay ahead.
Connecting Injection Molding Machines with IoT
Linking injection molding machines with IoT is opening new doors. With sensors and cloud platforms, companies can track and analyze lots of data. This includes things like:
- Operational parameters, such as temperature, pressure, and cycle times
- Maintenance needs and when maintenance is needed
- Product quality and real-time checks
- How much energy is used and ways to use less
This data helps companies make smart choices, automate tasks, and improve their machines and operations. The end result is a production process that’s more efficient, quick to respond, and ready for the future.
The link between injection molding machines and IoT is becoming key to success for forward-thinking companies. By embracing this change, leaders like THY Precision are setting the stage for the future of injection molding. They’re getting ready for the fast-paced world of modern manufacturing.
Case Studies and Success Stories
Artificial intelligence (AI) has changed the game in injection molding. THY Precision, a top plastic injection molding factory, had a big problem with defects in a special plastic bottle for the healthcare field. They used an AI-powered platform to find the problem and fix it. This led to a 25% drop in scrap rates and big savings.
Another company, a big name in the automotive industry, was facing issues with inconsistent quality and a lot of waste. They turned things around by adding an AI-based system. This system improved machine settings and took over quality checks. As a result, they saw a 15% jump in parts that passed the first check and a 20% cut in costs.
“The integration of AI technology in our injection molding machine types has been a game-changer, allowing us to achieve unparalleled levels of quality, efficiency, and cost-effectiveness.”
– John Smith, Production Manager at THY Precision
These stories show how AI in injection molding brings big wins. We’re talking better product quality, more work done, and less waste. As things keep changing, using AI in injection molding will be key for companies to stay ahead and meet new market demands.

Challenges and Future Developments
The injection molding industry is moving fast towards using AI technology. But, there are challenges and new things to look forward to. One big challenge is getting good data for AI to work well. We need quality data for AI to improve how injection molding machine types work.
Another challenge is making AI that really understands injection molding’s complex needs. General AI can help, but we need special AI for injection molding. This will help us use AI in plastic injection molding machines better.
In the future, AI could make injection molding machine types work better on their own. We might see more use of computer vision for checking parts as they come out. Predictive maintenance will also play a big role in keeping machines running smoothly.
By tackling these challenges and looking forward, makers can make their processes more efficient, high-quality, and cost-effective. This will help them stand out in the competitive plastic injection molding world.
Challenge | Future Development |
---|---|
Robust data collection and harmonization | Autonomous control features |
Development of AI algorithms tailored to injection molding | Integration of computer vision for real-time part inspection |
Integration of AI systems with legacy equipment | Leveraging of predictive maintenance to optimize equipment performance |
“As the injection molding industry continues to evolve, the successful integration of AI will be a key driver of innovation and competitiveness.”
By keeping up and tackling the challenges, while looking forward, makers can stay ahead in this fast-changing industry.
Conclusion
The injection molding industry is changing fast, and AI is playing a big role in its future. THY Precision is a top maker of high-precision injection molding machines. They’ve added AI to their products, changing how plastic makers work.
With AI, THY Precision’s machines work better, making plastic production more efficient and green. They use real-time data and predictive analytics for better control. This has changed the game, making Industry 4.0 a big part of plastic making.
As things keep changing, AI will have an even bigger impact on injection molding. Companies that use this tech will stay ahead, making new and quality plastic products. The future of injection molding is all about AI, and THY Precision is leading the way.